Acerca de
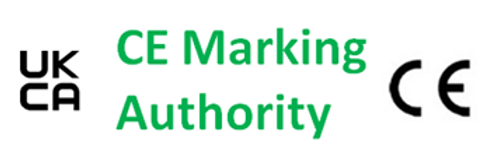
UK law on the design and supply of products
Brief details are provided on the main UK product safety legislation concerning the design and construction of equipment primarily for use at work, and some of the related supply legislation affecting similar consumer goods. More detailed information on each set of regulations can be found using the links provided below..
Most of this product supply legislation has common:
-
definitions for the terms used, like Economic Operators manufacturer, importers, distributor, authorised representatives, placing on the market,
-
common obligations on the various economic operators, especially for safety
-
when placing or making goods available on the market, including
-
meeting essential requirements
-
showing this in a technical file
-
the provision of information to the user
-
issuing a (in some cases of Performance, or Incorporation)
-
marking and labelling of the product to enable traceability
Products intended for the UK market must comply with the requirements of all applicable UK legislation, including those listed below, which require UKCA marking instead of CE marking in order to be placed on the market in GB. These documents which are used to demonstrate conformity is known as the Technical Construction File Use link below
However, products in conformity with relevant European product supply legislation and correctly bearing the CE marking will (until 31st December 2024) be treated as satisfying the requirements of the relevant UK legislation and need not bear UK marking.
Products intended for the single European market must comply with the requirements of European legislation. Use the following link; CE Marking
UK product legislation continues to align with many of those EU requirements and follows the same principles for demonstrating compliance to the legislation.
Contents
UK Legislation
Section 6 of the Health and Safety at Work etc Act 1974 (HSW Act)
Section 6 of the HSW Act applies to articles and substances for use at work where other more specific product safety law does not apply In particular, section 6 applies to:
-
intermediate suppliers of machinery for use at work
-
the second-hand supply of products for use at work, including those first placed on the market before relevant product safety regulations came into effect (unless so substantially refurbished/modified as to be considered 'new' under any of the applicable product safety regulations)
-
the hiring out of equipment for use at work
-
fairground equipment
Section 6(1) of the HSW Act places a general health and safety obligation on anyone in the supply chain, so far as reasonably practicable, for when articles for use at work are being used, set, cleaned or maintained. This obligation includes providing information and instructions on safe use, including any subsequent revisions to that information, and testing/examination necessary to ensure compliance. Enforcement of section 6 of the HSW Act is undertaken by HSE.
Supply of Machinery (Safety) Regulations
Machinery in brief. Most new machinery is covered by the Supply of Machinery (Safety) Regulations 2008 (and the Supply of Machinery (Safety) (Amendment) Regulations 2011 which added environmental aspects, but only for machinery applying pesticides). Their scope extends to other non-machinery products as defined including: safety components, interchangeable equipment, lifting accessories, chains, rope and webbing, removable transmission devices and partly completed machinery, but excludes such items as domestic electrical machines, many road going vehicles (but not machinery mounted on them), and fairground equipment. Other products that fall within the definition of machinery but are not covered by these regulations are toys and medical devices where more specific legislation applies (see below).
These regulations require that all machinery and other products in scope:
-
are designed and constructed to be safe, meeting all of the relevant essential health and safety requirements (EHSRs) listed in the regulations (they are supported by many British, European and International standards go to the UKs dedicated standards list
-
have a technical file compiled, and made available to the authorities when required, showing how the EHSRs are met
-
have appropriate conformity marking, and are correctly labelled with either the UKCA or CE mark
-
Are supplied with comprehensive instructions in English (or assembly instructions in the case of partly completed machinery)
-
are accompanied by a Declaration of Conformity (or, in the case of partly completed machinery, a Declaration of Incorporation)
Before they are placed on the market for the first time (or where not placed on the market, before being put into service for the first time). Subsequent use and maintenance is covered by PUWER. (This is the responsibility of the end-user)
These regulations apply to Responsible Persons (as defined), particularly manufacturers or their authorised representatives, and others such as:
-
importers of non-compliant equipment
-
distributors who market products under their own name
-
those who substantially modify existing machinery, or machinery and other products in scope before they are put into service
-
those who design and construct machinery for their own use
However, the regulations do not currently apply to most intermediate suppliers of machinery who are covered by section 6 of the HSW Act.
Some products which are in scope of the Supply of Machinery (Safety) Regulations (as amended) may also be covered by other product legislation in addition, including:
-
electrically powered/controlled machinery, where the Electromagnetic Compatibility Regulations (EMC) also apply
-
machinery incorporating radio equipment, where the Radio Equipment Regulations also apply
-
machinery incorporating pressure vessels, where the Pressure Equipment and/or Simple Pressure Vessels Regulations may also apply
-
construction products subject to the Construction Products Regulations which are machinery for incorporation in a permanent manner in construction works (buildings), such as powered gates, doors, windows, shutters and blinds, ventilation and air conditioning systems
-
non-road mobile machinery with combustion engines, where emissions are covered by the Non-road Mobile Machinery (Emission of Gaseous and Particulate Pollutants) Regulations
-
the Noise Emission in the Environment by Equipment for use Outdoors Regulations
Both HSE and local trading standards enforce the provisions of the Supply of Machinery (Safety) Regulations, depending on the field of use of the equipment (HSE leads where the product is for use at work).
Electrical Equipment Safety Regulations
The Electrical Equipment (Safety) Regulations 2016 as amended replaced the previous Electrical Equipment (Safety) Regulations 1994 on low-voltage equipment (most electrical equipment operating between 50-1000 volts alternating current and 75-1500 volts direct current). Machinery, with a few exceptions (household appliances for domestic use, some office equipment, electric motors and switchgear), which are subject to the Supply of Machinery (Safety) Regulations (as amended) are excluded from these electrical regulations, although the essential requirements and standards made to support these regulations can apply to electrically powered machinery by virtue of EHSR 1.5.1 of the Supply of Machinery (Safety) Regulations.
The Electrical Equipment (Safety) Regulations are supported by many designated standards and require that electrical equipment be appropriately marked and labelled, constructed to good engineering practice, and safe. These Regulations apply to manufacturers or their authorised representatives, importers and distributors all of whom now have a number of detailed and significant obligations to meet.
Both HSE and local trading standards enforce the provisions of these regulations, depending on the field of use of the equipment (HSE leads where the equipment is for use at work).
Pressure Equipment Regulations
The Pressure Equipment (Safety) Regulations 2016 and The Simple Pressure Vessels (Safety) Regulations 2016 (both as amended) replace the previous Pressure Equipment Regulations 1999 and Simple Pressure Vessels (Safety) Regulations 1991 (as amended in 1994). These regulations provide for the safety, by design and construction, of most pressure equipment and assemblies at a pressure of more than 0.5 bar.
HSE enforces the provisions of these regulations for equipment for use at work.
Duties for safety are placed on the manufacturer or their authorised representative, importers and distributors. Machinery may include pressure systems which come within scope of these regulations. In such cases, the requirements of these regulations apply to the pressure parts of the machine, alongside those requirements under the Supply of Machinery (Safety) Regulations for the machine.
The PE(S)R apply to pressure equipment and assemblies with a maximum allowable pressure PS greater than 0.5 bar, although there are a number of exclusions, which are set out in regulation 4 and Schedule 1 to the Regulations. “Pressure equipment” means vessels, piping, safety accessories and pressure accessories. “Assembly” means several pieces of pressure equipment assembled to form an integrated, functional whole.
In order to know how the PE(S)R apply to specific items of pressure equipment, the manufacturer will need to know:
-
the type of equipment concerned, i.e. vessel, steam generator or piping
-
the state of the intended fluid contents – gas or liquid and
-
the fluid group of the intended contents – Group 1 or Group 2.
Group 1 comprises those substances and mixtures
-
unstable explosives or explosives of Divisions 1.1, 1.2, 1.3, 1.4 and 1.5
-
flammable gases, category 1 and 2
-
oxidising gases, category 1
-
flammable liquids, category 1 and 2
-
flammable liquids, category 3 where the maximum allowable temperature is above the flashpoint
-
flammable solids, category 1 and 2
-
self-reactive substances and mixtures, type A to F
-
pyrophoric liquids, category 1
-
pyrophoric solids, category 1
-
substances and mixtures which in contact with water emit flammable gases, category 1, 2 and 3
-
oxidising liquids, category 1, 2 and 3
-
oxidising solids, category 1, 2 and 3
-
organic peroxides types A to F
-
acute oral toxicity, category 1 and 2
-
acute dermal toxicity, category 1 and 2
-
acute inhalation toxicity, category 1, 2 and 3
-
specific target organ toxicity – single exposure, category 1
Assistance with identifying the hazard classes of substances can be found by contacting the team at the CE Marking Authority
Group 1 also comprises substances and mixtures contained in pressure equipment with a maximum allowable temperature TS which exceeds the flashpoint of the fluid.
Group 2 comprises substances and mixtures not referred to under group 1, within the definition of a fluid, including steam.
With this information the manufacturer can identify the relevant conformity assessment table in Schedule 1B to the PE(S)R and determine the correct classification of the equipment by plotting the maximum allowable pressure and, in the case of vessels, the volume in litres or, for piping, the nominal size (DN).
Equipment and assemblies which are below or equal to the limits set out in regulations 6(a)-(c) or 7 of the PE(S)R must be designed and manufactured in accordance with sound engineering practice in order to ensure safe use and must be accompanied by adequate instructions for use. Unless required by other applicable legislation, this second category of equipment and assembly must not bear the UKCA mark. This is set out in regulation 8 of the PE(S)R.
Simple Pressure Vessels (Safety) Regulations
The Regulations apply to simple pressure vessels manufactured in series with the following characteristics:
-
The vessels are welded, intended to be subjected to an internal gauge pressure greater than 0,5 bar and to contain air or nitrogen, and are not intended to be fired;
-
The parts and assemblies contributing to the strength of the vessel under pressure are made either of non-alloy quality steel or of non-alloy aluminium or non-age hardening aluminium alloys;
-
The vessel is made of either of the following elements:
-
a cylindrical part of circular cross-section closed by outwardly dished and/or flat ends which revolve around the same axis as the cylindrical part; and
-
two dished ends revolving around the same axis;
-
-
The maximum working pressure of the vessel does not exceed 30 bar and the product of that pressure and the capacity of the vessel (PS × V) does not exceed 10 000 bar.L; and
-
The minimum working temperature is no lower than – 50 °C and the maximum working temperature is not higher than 300 °C for vessels constructed of steel and 100 °C for aluminium or aluminium alloy vessels
Equipment and Protective Systems Intended for Use in Potentially Explosive Atmospheres Regulations
The Equipment and Protective Systems Intended for Use in Potentially Explosive Atmospheres Regulations 2016 (as amended) replaced the previous Regulations 1996, as amended in 2001 and 2005, and are usually known as ATEX but in the UK its is now known as the UKEX, for equipment and protective systems intended for use in explosive atmospheres. Safety, controlling and regulating devices intended for use outside potentially explosive atmospheres - but still contributing to the safe functioning of equipment / protective systems against explosion - also come within scope of the regulations. In addition to marking and labelling in common with other product legislation. ATEX equipment must normally bear the specific explosion protection mark - Fig 1.
Manufacturers or their authorised representative, importers and distributors must meet the requirements for safety. ATEX components (eg a rotary valve) may be incorporated within other products (eg dust extraction machinery). In such cases, the machine may be supplied with an additional Declaration of Conformity, relating specifically to the ATEX component.
The 2016 Regulations apply to equipment and protective systems intended for use in potentially explosive atmospheres as defined in regulation 3.
Specifically, the Regulations relate to:
-
equipment intended for use in potentially explosive atmospheres, defined as machines, apparatus, fixed or mobile devices, control components and instrumentation thereof and detection or prevention systems which, separately or jointly, are intended for the generation, transfer, storage, measurement, control and conversion of energy or the processing of material and which are capable of causing an explosion through their own potential sources of ignition;
-
protective systems intended for use in potentially explosive atmospheres, defined as devices which are intended to halt incipient explosions immediately and/or to limit the effective range of explosion flames and explosion pressures. Protective systems may be integrated into equipment or separately placed on the market for use as autonomous systems;
-
safety devices, controlling devices and regulating devices intended for use outside potentially explosive atmospheres but which are required for or contribute to the safe functioning of equipment and protective systems, with respect to the risks of explosion; and
-
components defined as any item essential to the safe functioning of equipment and protective systems but with no autonomous function.
Electromagnetic Compatibility Regulations
The Electromagnetic Compatibility Regulations 2016 (as amended) replace the Electromagnetic Compatibility Regulations 2006, as amended 2006, and concern the avoidance of undue electromagnetic disturbance generated by electrical equipment, and the sufficient immunity of electrical equipment against electromagnetic disturbance. As most machinery are electrically powered, it will have to meet these requirements in addition to those under the Machinery Directive 2006/42/EC. HSE does not have a role in respect of these Regulations, even for industrial equipment, and most enforcement falls to the relevant local trading standards service. Note the EMC requirements can be meet by testing or putting justification in the technical file detailing how the regulations have been met.
The aim of employing EMC measures is to ensure that a variety of different items of electronics equipment can operate in close proximity without causing any undue interference.
The interference that gives rise to impaired performance is known as Electromagnetic Interference, EMI. It is this interference that needs to be reduced to ensure that various items of electrical equipment are compatible and can operate in the presence of each other
There are two main elements to EMC:
-
Emissions: The EMI emissions refer to the generation of unwanted electromagnetic energy. These need to be reduced below certain acceptable limits to ensure they do not cause any disruption to other equipment.
-
Susceptibility & immunity: The susceptibility of an item of electronics to EMI is the way it reacts to unwanted electromagnetic energy. The aim of the design of the circuit is to ensure a sufficiently high level of immunity to these unwanted signals.
The Radio Equipment Regulations 2017 (where amended) which replaced the Radio Equipment and Telecommunications Terminal Equipment Regulations 2000, as amended in 2003 Radio Equipment and Telecommunications Terminal Equipment Regulations 2000 amendments & 2003 Radio Equipment and Telecommunications Terminal Equipment Regulations 2000 amendments 2, concern the safety and interference with other radio equipment. Where electrical equipment incorporates radio equipment as defined, the Electrical Equipment Safety Regulations 2016 and Electromagnetic Compatibility Regulations 2016 do not apply: instead the safety and functional objectives from them are subsumed into the Radio Equipment Regulations. Enforcement of these Regulations falls to the relevant local trading standards service even in the case of radio equipment for use at work, or OFCOM in the case of the protection and management of the radio spectrum.
The UK Radio Equipment Regulations apply to all equipment placed on the market in Great Britain that uses the radio spectrum below 3THz for communication and for radiodetermination. The regulations apply to both transmitters and receivers. This means that if you manufacture any product that transmits or receives radio frequencies over the air your product will almost certainly be subject to the Regulations.
This includes connected devices such as those that transmit and receive radio signals including WiFi and Bluetooth devices. This could include medical devices, fire detection and suppression products, or many other products used throughout the built environment.
General Product Safety Regulations
The General Product Safety Regulations 2005 (where amended) concern consumer products which are not covered by any other product legislation. Enforcement of these regulations falls to the relevant local trading standards service.
Where a product is already subject to other existing regulations (for example, toys) then those regulations will apply to that product. The GPSR do not apply to the safety of a product where there are specific provisions of UK law governing all aspects of its safety; instead, they operate as a kind of 'mop-up' set of regulations.
However, they do apply to all second-hand consumer products, including toys and electrical equipment.
The GPSR do apply where they go further than the existing regulations in terms of the specific aspects of safety covered and the extent of the obligations on producers. The GPSR apply to all products intended for or likely to be used by consumers (even if not intended for them) that are supplied or made available; the test would be whether a consumer can purchase the product without challenge. This includes products supplied or made available to consumers for their own use in the course of a service
The Restriction of the Use of Certain Hazardous Substances in Electrical and Electronic Equipment Regulations 2012 (as amended) restrict the use of certain hazardous materials (lead, cadmium, mercury, etc) in the manufacture of various types of electronic and electrical equipment. The Office for Product Safety and Standards enforces the provisions of these regulations.
Ecodesign for Energy-Related Products Regulations
The Ecodesign for Energy-Related Products Regulations 2010 (as amended) aim to improve the environmental performance of products throughout their life-cycle, starting at a very early stage in their design. Enforcement of these regulations falls to the Office for Product Safety and Standards.
BEIS guidance on Ecodesign of energy-related products
If you require UKCA Marking assistance Contact the team below;
CE Marking Authority
Tomorrows Certification Today
Tel: +44 (0) 1779 841842
Tel; +44 (0) 7910 523528